Kanban systems are an important inventory control mechanism in manufacturing. Kanban is a Japanese word that directly translates to "visual card", so a kanban system simply means to use visual cues to prompt the action needed to keep a process flowing. These systems are used in manufacturing to indicate when inventory is running low at a particular production line or station so that it can be replenished to prevent any production downtime at the station.
Traditional kanban systems rely on material visual cues such as cards or flags that are raised when inventory is low. Kanban systems differ from poka-yoke systems in that poka-yoke systems are used to prevent errors in production while kanban systems are for avoiding production halts due to a shortage of parts. However, the more modern kanban systems involve the use of electronics to produce digital signals indicating low inventory.
While the modern electronic kanban systems are an upgrade on the traditional ones, they still possess implementation challenges. A much better approach is to use computer vision for tracking inventory for kanban systems as this method costs far less than electronic systems while producing equivalent or better results.
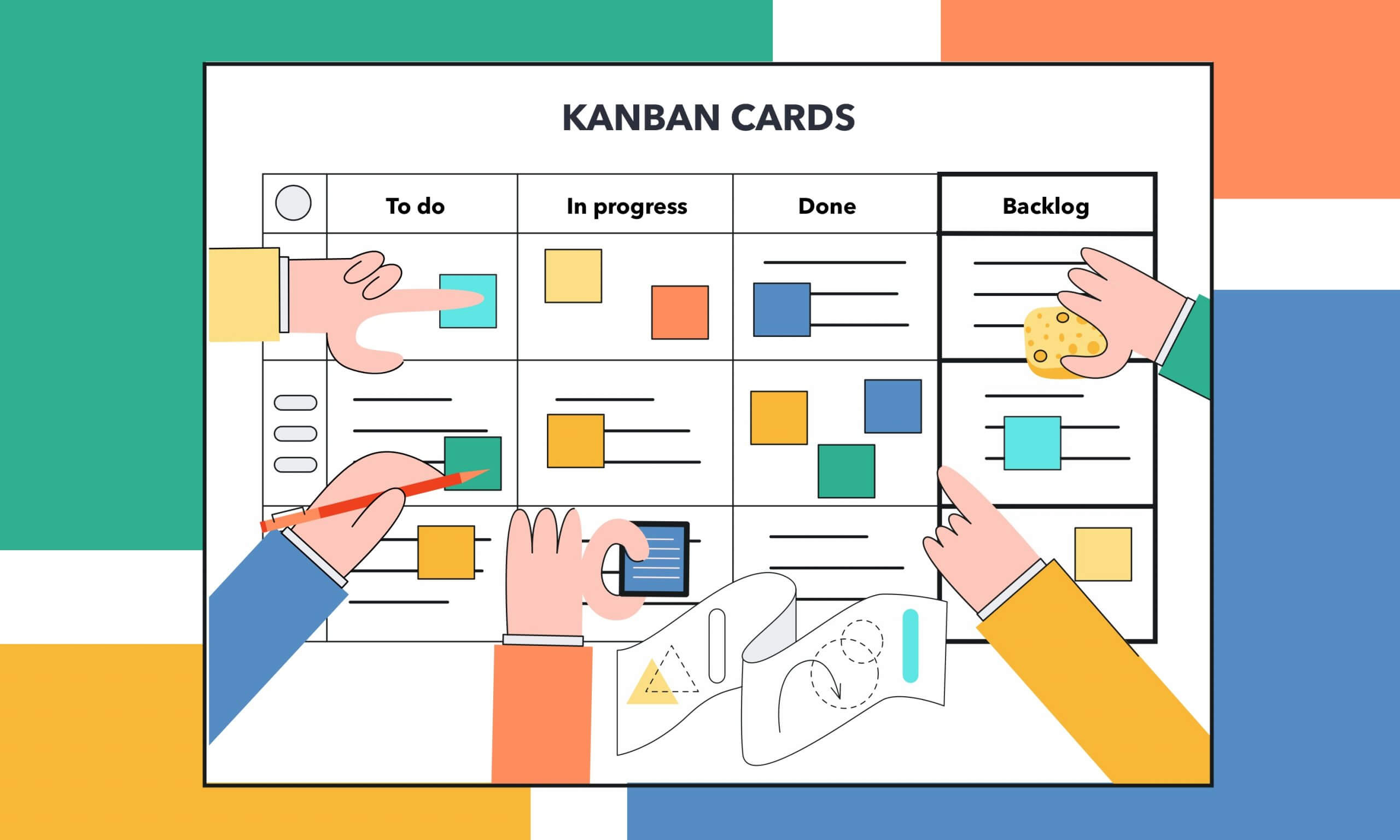