Defects are a common occurrence in manufacturing and can be minimized but not completely avoided. However, it is imperative for manufacturers to catch these defects as early as possible in the manufacturing process to prevent catastrophic problems down the road. For example, for an automotive OEM preventing defects or catching defects early in the car assembly process can potentially prevent the recalls of millions of vehicles that can cost the company hundreds of millions of dollars in warranty and repair costs. In the worst case recalls can cost an auto company to go bankrupt. Poka-yoke is one of the most effective ways of avoiding defects in manufacturing.
The Japanese term poka-yoke means “mistake proofing” or “error prevention”. It is the use of any automatic device or method that either makes it impossible for an error to occur or makes the error immediately obvious once it has occurred. It is a common process analysis tool in manufacturing. Poka-yoke is important because it helps manufacturers avoid production defects or catch them quickly to prevent potential catastrophic issues down the road. While current poka-yoke systems are effective, they are unable to capture all errors (resulting in more potential defects in the final product).Digital poka-yoke systems are much better at capturing a larger number of assembly errors so they can be corrected in real time, resulting in a more cost effective process in the long run.
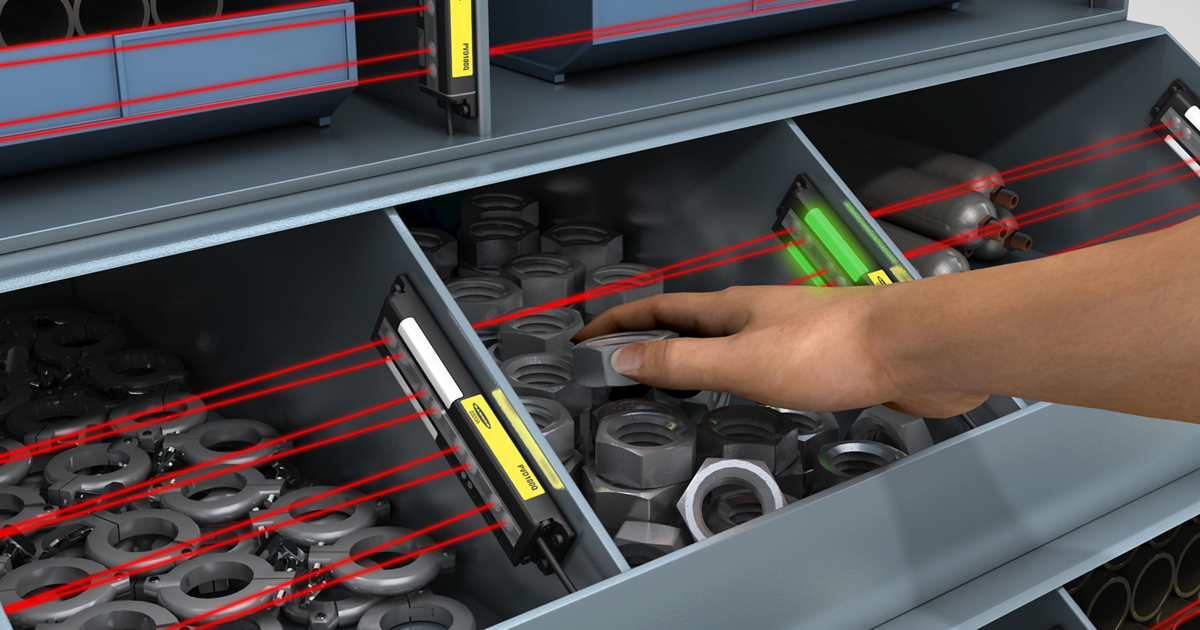