The COVID-19 pandemic has changed the way many industries operate, and manufacturing is no exception. While the majority of manufacturing employees were unable to work remotely during the pandemic, about 41% were able to adopt remote work. Now, as companies are beckoning employees back to the office, manufacturers are strategizing how to integrate work-from-home policies to boost retention and attract top talent.
“I talk to a lot of manufacturing leaders who want to enable flexibility and remote work to attract the best talent,” said Carolyn Lee, president and executive director of the Manufacturing Institute. “The conversation has really evolved to where flexibility is key and very much an essential ingredient for attracting and maintaining a workforce.”
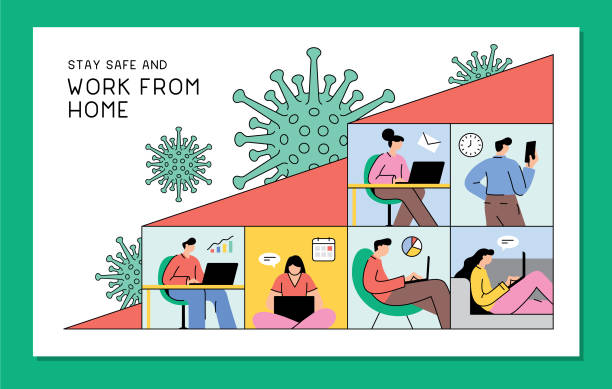